Intercol has been working successfully for many years to improve the bonding process at customers. The future vision of Intercol is “zero defects”. In the past year Intercol, together with several customers, has again made great strides with regard to this vision. The combination of Intercol’s know-how in the bonding process and with its Superjet 900 cold adhesive has resulted in a significant reduction in the number of bonding problems with its customers.
Strong quality thanks to new cold adhesive
The end users of cardboard boxes also challenge producers of cardboard boxes to improve the bonding process. Millions of boxes often go through each month, but if there are 10 individual, incorrectly produced boxes in between, that’s too many. Every stop in a high speed production line costs time and a lot of money’, explains a production manager in the corrugated board industry. Stops on the machine and quality problems are often a reason to take a close look at the gluing process. Other glue suppliers are also taking steps, but things had to get even better. In the end they succeeded together with Intercol. The number of errors has decreased from a few dozen to one to two per quarter. And those errors are usually not due to the glue’.
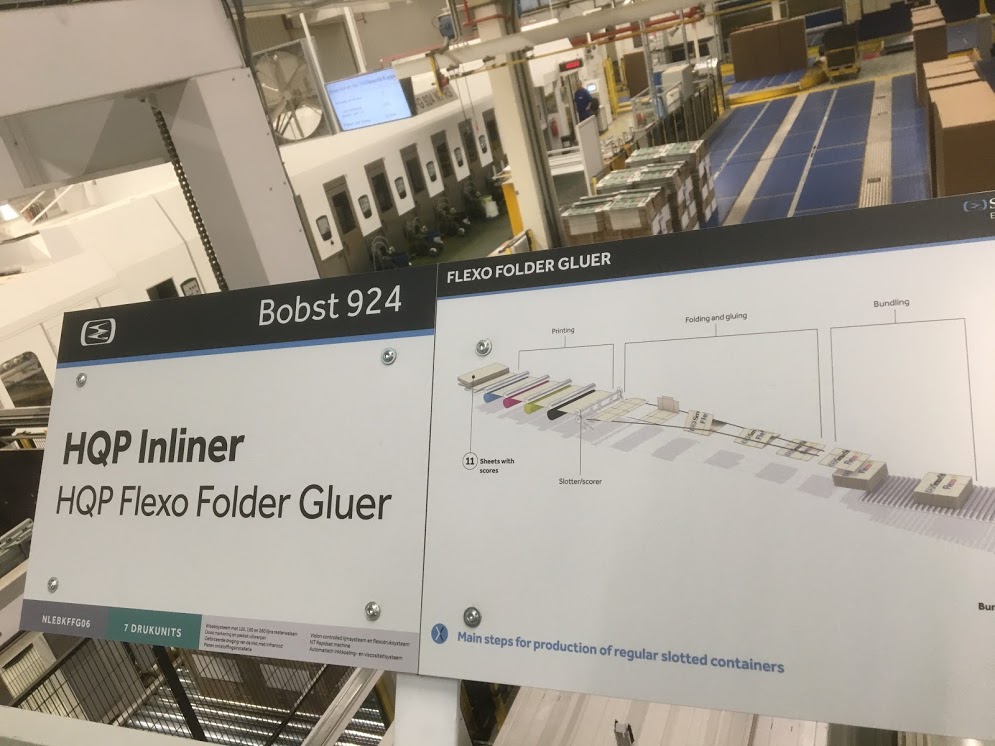
Automation is a key factor and important parameter for gluing
What also plays a role in many complaints is that the packaging processes are becoming more and more automated, ‘The far-reaching automation at customers demands good quality boxes. The box erectors are listening more and more closely. A wrongly glued box can paralyse a production line. That is why it is very important that every box is produced perfectly. Glue on the inside or outside of the box causes the so-called inside or outside sticking respectively. At the first mentioned problem, the box does not fold open and at the other the boxes stick together. As a result, the production stops and the customer makes a claim. The need to improve gluing processes has increased due to increasing automation’.
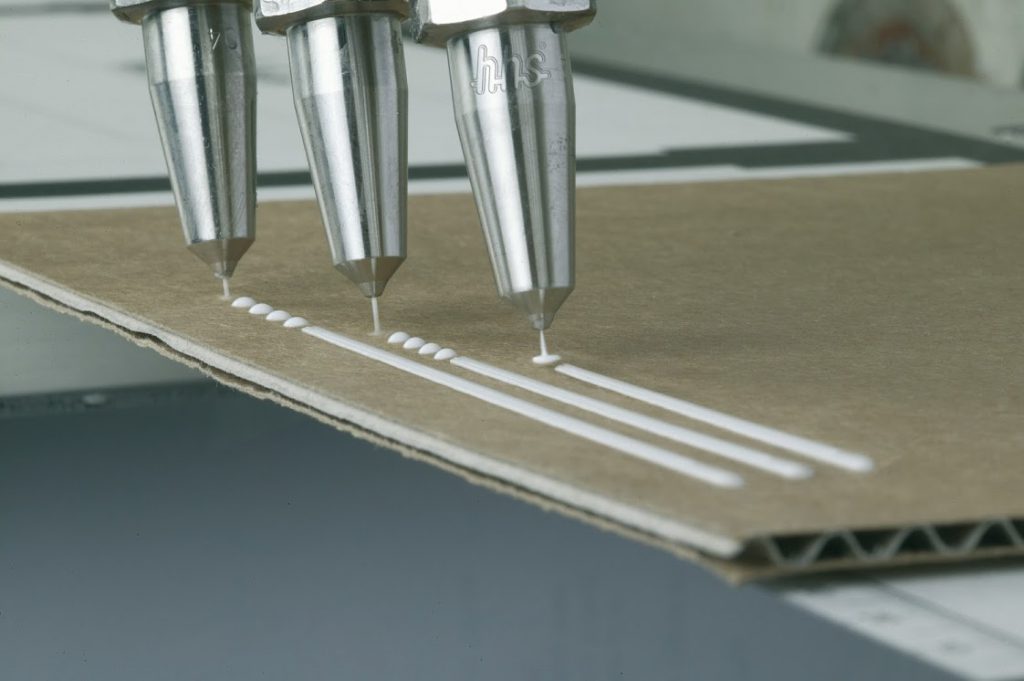
Replacing an adhesive is a major step
A corrugated board manufacturer does not simply switch to another adhesive supplier’, ‘You take a risk with this and changes often attract resistance. People are conservative.’
At one of our customers a pilot on one of the five inliners was tested with the Superjet 900 adhesive from Intercol. Two parameters were important: the adhesive behaviour and the number of micro stops of the carton folding machine.
The adhesive behaviour, the adhesion, was not a problem with any of the adhesives’, ‘But we saw big differences in the number of microstops’. With the Intercol adhesive there are 28% fewer microstops. An important advantage, because every machine stop is a potential complaint. Fewer stops makes our process much more stable. In fact, you create a quarter less complaints with it’.
This quickly dispelled the staff’s doubts about the new adhesive. Operators, technical service and the quality department were all upset’.
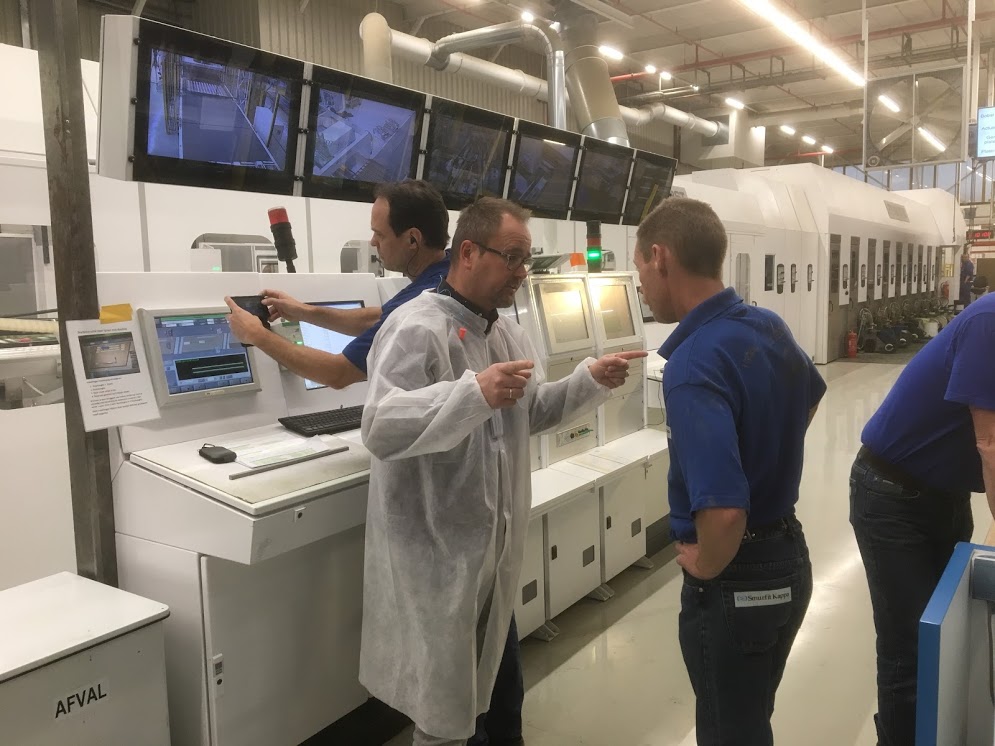
It starts with the right viscosity
“Producing a good box starts with the basics. So with good cardboard and good glue’, says a technical sales manager at Intercol. That glue has to be applied with a constant quantity and that requires a controlled process. If the viscosity of the glue is too high, the dosage is inaccurate. If the viscosity is too low, the glue drips off the boxes and the box does not adhere well’.
The viscosity of adhesives can be influenced, among other things, by the outside temperature. If adhesive pipes run under the roof, where it can be very cold in winter and the temperature can rise to 40 degrees Celsius in summer, while the adhesive has been developed for processing around 20 degrees Celsius. Operators often adjust the process by adjusting the adhesive pressure or needle stroke to the conditions.
Local technical support on adhesive systems
Manually adjusting the settings makes the process unstable’, ‘We have therefore introduced another adhesive with its viscosity, which has been developed for processing on non-contact adhesive systems and recommends a linear adhesive pressure curve that is linked to the machine speed. This ensures that the glue pressure always matches the speed. At start-up, the machine runs at about 20 metres per minute and little pressure is required. If the machine is running at full speed, about 400 metres per minute, then the adhesive pressure has to increase considerably. Such an adhesive curve creates calm for the operator and reduces the risk of errors’.
Finally, an average higher viscosity results in less splashing and the nozzles are reduced from size 6 to size 4.
Food safety and optical brighteners
A further advantage of the new Superjet 900 adhesive is that it is detectable on white and recycled cardboard, so that detection systems can see the adhesive. Optical brighteners in cardboard can cause problems with standard detection agents,” explains Intercol. Our adhesive contains a food-safe detection dye. This is unique because many adhesive manufacturers usually exclude the UV dye from the food safety declaration’.
Looking back and forward.
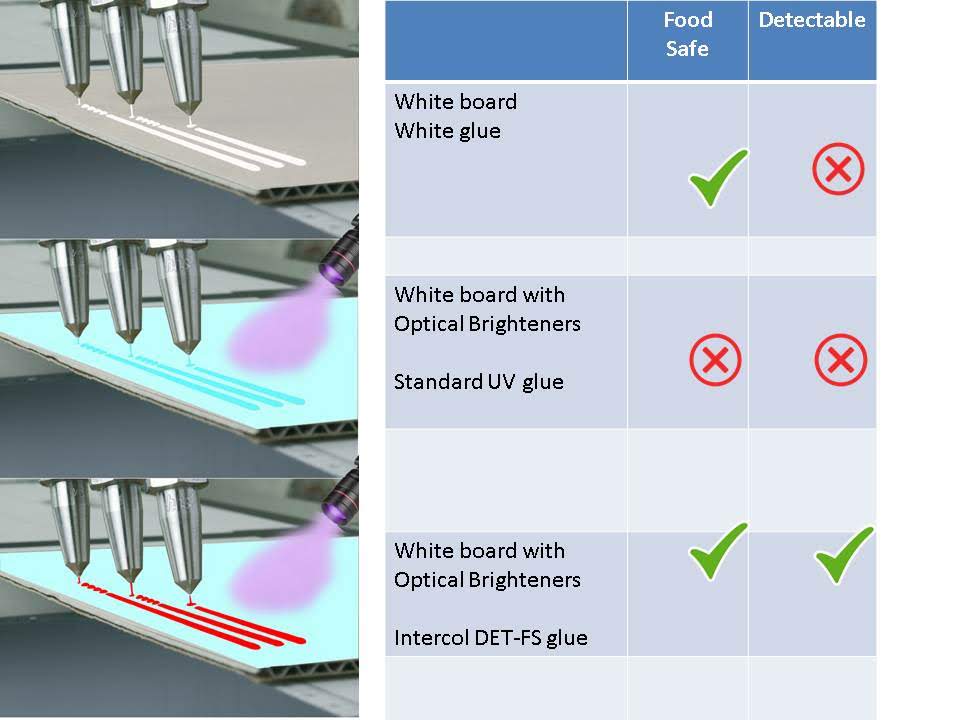
For a corrugated board manufacturer it’s a major step to change cold glue,’ stresses one of Intercol’s customers. ‘Intercol’s patience and persuasiveness has resulted in a good result. In addition, as an adhesive supplier, Intercol does not run away from problems and also dares to think ‘out of the box’. Intercol’s broad knowledge of the different adhesive systems on the machines and the good contact with the operators has contributed to the success of this project’.
Intercol reduces gluing problems on Turbox folder gluer
‘This project is a good step in our zero defect vision and a good addition to our already invested in process control resources’ is the opinion of a production manager of the processing department at a cardboard factory. But of course we are trying. A lot has been invested in optimisation and where we want to go is in controlling and adjusting process behaviour better and better’.
In addition, an integrated approach is important. We also look at the client’s set-up process and think along with them. It’s all about a joint approach with customers and suppliers. The goal of box manufacturers is ultimately to satisfy customers who have fewer malfunctions on their machines.